#1 Ranking: Read how InetSoft was rated #1 for user adoption in G2's
user survey-based index
|
|
Read More
|
Inventory KPI
A warehouse is for stocking products which are known as inventory. The inventory KPI deals with how much you
have stocked and how much is being dispatched. So, the important KPIs in inventory are:
- Inventory Accuracy - The products present in the warehouse must match the products tracked by the
inventory tracking system. If there is a mismatch, it means that there is a miscalculation, theft, damage,
or any other fault from the supplier. So, this Inventory accuracy helps to find out the difference between
the physical stock and the tracked stock.
- Carrying Cost - This evaluates the total money spent on owning, storing, and maintaining an inventory. If
this value is too much, it means that you are losing your investment because of slow-moving products and
dead stock. So, with KPI, you can recognize this issue and find a solution.
- Inventory Turnover - This determines the speed at which your inventory is selling. If this turnover value
is less, it may indicate that the sales are weak. You can start developing strategies to increase sales and
increase turnover.
Receiving KPI
In order to have an inventory, you need to receive goods or products from a supplier. Only then you can sort,
and store them. So, the receiving KPI deals with the efficiency of receiving and the effectiveness of the
process. The important KPIs in receiving are:
- Receiving Efficiency - This KPI can help you find out the efficiency of your employees in receiving the
inventory. It is determined by dividing the volume of inventory received by the number of man hours.
- Receiving Cost per Line - This finds out the total cost spent on each receiving line. The cost includes
money spent on handling, accounting, etc. This KPI is calculated by dividing the total cost spent on
receiving by the number of items on each receiving line.
- Receiving Cycle Time - This is an important factor that helps you to know how much time is spent in the
entire process of receiving. This includes sorting, accounting, handling, etc. This can be found by dividing
the total time spent by the total number of items received.
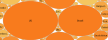 |
Read how InetSoft saves money and resources with deployment flexibility. |
Putaway KPI
Proper storing techniques are very important in every warehouse. If you don't manage it, the efficiency of
the warehouse will be drastically affected. The cost will also increase a lot and you cannot control it. So,
the inventory you receive must be stored appropriately, and measuring its performance is done by the Putaway
KPI. The important KPIs in putaway are:
- Accuracy - This indicator is used to determine the proportion of items putaway properly after they have
been received at the warehouse. It is calculated by dividing the number of inventories stored correctly by
the total number of inventories putaway. Getting a value of more than one indicates a mistake in storing.
- Putaway Cost per line - Knowing how much it costs to putaway items in each line is important. This is
determined by dividing the total cost of putaway by the total line.
- Putaway Cycle time - In order to increase efficiency, you need to reduce the time. This KPI can help you
to know the average time required to putaway an item in your inventory. If you are able to putaway items in
a shorter time, you can improve the overall warehouse efficiency.
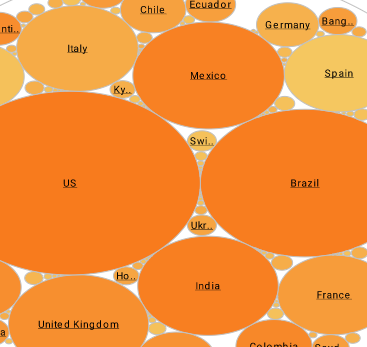 |
“Flexible product with great training and support. The product has been very useful for quickly creating dashboards and data views. Support and training has always been available to us and quick to respond.
- George R, Information Technology Specialist at Sonepar USA |
Order Management KPI
Order management involves all the processes happening from the time a customer places an order and receives
the item in their hands. Order acceptance, picking the right item according to the order received, the package
of items, shipping, and post-sales processes are included in the order management. This KPI lets you determine
how effectively each process takes place. The important KPIs in order management are:
- Order Cycle Time - It determines the average time taken for an order to reach the customer and consists of
the time taken for each process since order placement. It includes accepting time, picking time, packing
time, and shipping time. A shorter time leads to more repeat customers.
- Backorder Rate - This determines the number of returns placed compared to the total number of orders
received. Having a higher rate of backorders can affect your warehouse severely with respect to cost, time,
and efficiency.
- Fulfillment Rate - This indicates the number of orders that have been completed successfully right from
order placement to the receiving of the item by the customer. To calculate this, you have to divide the
orders completed without any issues by the total orders received.
Safety
Warehouse accidents happen at times and you need to ensure the safety of your employees and the items in your
inventory. So, in order to measure the safety parameters of your warehouse, this KPI can help you find out
where you lack. The important KPIs in safety are:
- Total number of Accidents Per Year - This factor will show you the number of accidents that occur per year
and you can take heed of it to bring changes to the safety measures.
- Time since last accident - This KPI lets you know the time gap between the last accident and you need to
keep this number high.
Conclusion
The performance of a warehouse can be improved only by proper management. These KPIs will provide you with
the proper data and gives an insight into where to improve your process efficiency. By taking note of each of
these indicators you can run a warehouse successfully.