#1 Ranking: Read how InetSoft was rated #1 for user adoption in G2's user survey-based index |
|
Read More |
Overall Equipment Effectiveness (OEE)
The Overall Equipment Effectiveness indicator assesses both the effectiveness of the production process and the performance of industrial equipment. It has three crucial elements:
- Availability: This KPI evaluates equipment uptime by calculating the proportion of time it is accessible for production. Availability may be impacted by downtime brought on by repairs, malfunctions, or transitions.
- Performance: The speed at which equipment functions in relation to its optimum capacity is measured by the performance KPI. It assesses variables such as cycle duration, output rate, and equipment dependability.
- Quality: The rate of production from manufacturing equipment that is free of defects is the focus of the quality KPI. It keeps track of the proportion of goods that fulfill quality requirements.
Cycle Time and Throughput
Cycle time is the overall amount of time needed to complete one cycle of a certain manufacturing process. Cycle time is a tool that manufacturing operations analysts use to identify bottlenecks, restructure workflow, and enhance output. Contrarily, throughput describes the volume of output a manufacturing facility generates in a certain length of time. Analysts may evaluate the manufacturing line's productivity and capacity using these parameters.
Yield
Yield is a crucial KPI that assesses the proportion of items that fulfill quality criteria to determine how well the manufacturing process is working. Operations analysts can identify problem areas, enhance production conditions, and save waste by monitoring yield.
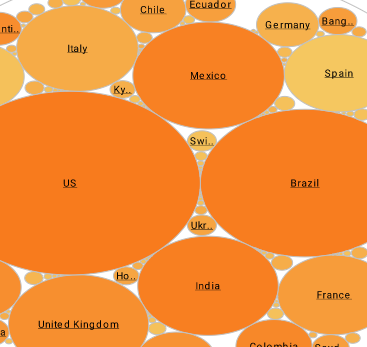 |
“Flexible product with great training and support. The product has been very useful for quickly creating dashboards and data views. Support and training has always been available to us and quick to respond.
- George R, Information Technology Specialist at Sonepar USA
|
Inventory Turnover
Inventory turnover is a measure that determines how often inventory is sold or utilized over a certain time frame. It assesses inventory management effectiveness and shows how rapidly raw resources are transformed into final commodities. Analysts can spot excess inventory levels, save holding costs, and improve procurement and production planning by keeping track of inventory turnover.
Downtime and Mean Time Between Failures (MTBF)
Equipment downtime is the time when manufacturing machinery is not in use. Manufacturing operations analysts monitor downtime to determine the reasons for equipment failures, their frequency, and the need for maintenance and replacements. This information aids in enhancing device dependability and decreasing unscheduled downtime.
The average interval between equipment failures is measured by Mean Time Between Failures (MTBF). It aids analysts in understanding the performance and dependability of equipment, identifying trouble spots, and enhancing maintenance plans.
Cost of Goods Sold (COGS) and Overall Cost Efficiency
COGS is a measure of the direct expenses incurred in the production of products, such as labor, overhead, and raw materials. Manufacturing operations analysts look at COGS to find ways to cut costs, improve production methods, and boost profitability.
A more comprehensive indicator that assesses the cost-effectiveness of manufacturing activities overall is called overall cost efficiency. To promote cost reductions, it takes into account variables including resource allocation, waste reduction, energy use, and process optimization.
Employee Productivity and Labor Utilization
Employee productivity is a gauge of how effectively labor is used throughout the production process. It evaluates the result produced per labor input unit. This statistic is used by operations analysts to pinpoint training requirements, enhance worker distribution, and boost overall labor productivity.
The level of labor utilization indicates how well the labor force is put to use during manufacturing. Analysts can spot overstaffing or understaffing issues, improve shift scheduling, and guarantee effective resource allocation by looking at labor usage.
Scrap and Rework Rates
The proportion of flawed goods or parts that are thrown away during production is known as the scrap rate. The proportion of faulty products that are fixed and reprocessed is measured by the rework rate, on the other hand. Operations analysts may find opportunities to enhance product quality, streamline workflow, and save waste using these data.
First-pass Yield (FPY)
The proportion of items that make it through the production process without needing any rework or repairs is known as first-pass yield. While a low FPY shows the need for process optimization or quality control enhancements, a high FPY implies efficient and effective manufacturing operations.
Supplier Performance
Manufacturing operations analysts must evaluate supplier performance. Metrics including on-time delivery, raw material quality, and adherence to requirements aid in determining a supplier's dependability. Analysts can identify possible supply chain bottlenecks, improve supplier relationships, and guarantee a steady flow of high-quality inputs by tracking supplier performance.
Work-in-Progress (WIP) Inventory
The quantity of unfinished goods or unassembled parts in the production process is measured by the WIP inventory. Longer lead times, higher carrying costs, and inefficiencies may result from high quantities of WIP inventory. WIP inventory is monitored by operations analysts to spot production bottlenecks, reorganize processes, and shorten cycle times.
Equipment Utilization
By calculating the proportion of time that a piece of manufacturing equipment is actively being utilized for production, equipment utilization assesses the efficacy and efficiency of that equipment. It enables analysts to maximize equipment productivity, manage maintenance schedules, and find idle or underused equipment.
Energy Consumption
A crucial KPI for sustainable industrial processes is energy usage. Analysts keep an eye on energy use to spot chances to boost energy efficiency, streamline manufacturing, and lessen the effect on the environment.
Compliance and Safety Metrics
The primary goals of compliance and safety metrics are to guarantee that legal requirements are followed and to keep the workplace safe. Manufacturing operations analysts monitor indicators including safety incidents, adherence to safety rules, and regulatory compliance to spot problem areas, put right the wrong things, and reduce risks.
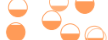 |
Read what InetSoft customers and partners have said about their selection of Style Report as their production reporting tool. |
Lead Time
From the time an order is received until it is delivered, the lead time is the amount of time it takes to fulfill the order. Lead time is analyzed by manufacturing operations experts to optimize production schedules, speed up order fulfillment, and improve customer satisfaction.
Customer Satisfaction
Customer satisfaction is a crucial performance metric that evaluates the standard of the goods offered, as well as their responsiveness, timeliness, and general quality. For the purpose of identifying opportunities for improvement, enhancing product quality, and fostering stronger customer connections, manufacturing operations analysts examine customer comments, ratings, and reviews.
Forecast Accuracy
The degree to which actual output and demand match the projections is known as prediction accuracy. To improve production planning, control inventory levels, and reduce supply chain interruptions, operations analysts check forecast accuracy.
Return on Investment (ROI)
The financial success of industrial activities is assessed by return on investment. It evaluates the return on investment and operational effectiveness of people, process, and technological initiatives. Manufacturing operations analysts use ROI analysis to prioritize investments, make data-driven choices, and promote financial success.
Manufacturing operations analysts may gather insightful information, identify areas for development, and promote operational excellence in the manufacturing process by using these KPIs and analytics.